Motor control printed circuit boards (PCBs) are the primary regulators for electronic motor function. They dictate how a motor performs within specific parameters and allow operators to make adjustments based on the task at hand. In short, PCBs control the function of a motor. When faults develop, they affect the controller’s efficacy and present hazards for operators and equipment alike.
Motor control boards are specialized circuit boards designed for the purpose of controlling and driving electric motors. These PCBs are used in a wide range of applications, from industrial automation and robotics to consumer electronics and automotive systems. They play a critical role in regulating motor functions, ensuring efficient and precise control. Here are some key features and functions associated with motor control PCBs:
Power Regulation: Motor control PCBs provide the necessary power regulation to ensure the motor receives the correct voltage and current for its operation. They often include voltage regulation circuits and current control mechanisms.
Motor Type Compatibility: These PCBs are designed to work with specific types of motors, such as DC motors, stepper motors, servo motors, or brushless DC motors. The PCB’s design and components may vary depending on the motor type.
Signal Processing: Motor control PCBs process input signals to determine the motor’s direction, speed, and position. They often include microcontrollers or dedicated motor control ICs (integrated circuits) for this purpose.
Feedback Systems: In advanced applications, motor control PCBs can integrate feedback mechanisms, such as encoders or sensors, to provide closed-loop control. This allows for precise control of motor positioning and speed.
Communication Interfaces: Many motor control PCBs have communication interfaces, such as UART, SPI, or CAN, for external communication with other control systems or microcontrollers. This enables the integration of the motor into larger systems.
Safety Features: Motor control PCBs often include safety features like overcurrent protection, over-temperature protection, and short-circuit protection to prevent damage to the motor and the control electronics.
PWM Control: Pulse width modulation (PWM) is commonly used to control the speed of motors. Motor control PCBs may include PWM generators for precise speed control.
Software Control: Some motor control PCBs are programmable and allow for software-based control and customization of motor parameters.
Compact Design: These PCBs are typically designed to be compact and integrate seamlessly into the overall system, making them suitable for various applications with space constraints.
MultiAxis Control: In applications where multiple motors need to be controlled simultaneously (e.g., robotics), motor control PCBs can support multi-axis control for coordinated movements.
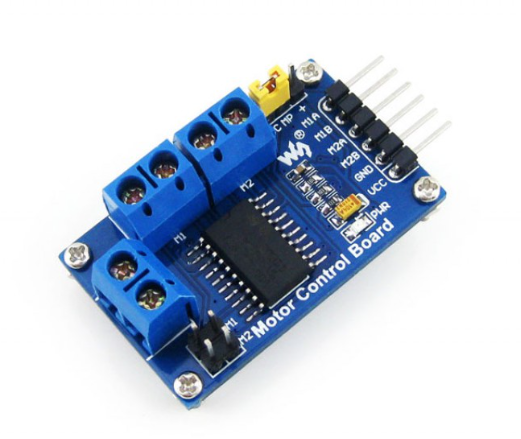
Motor control PCBs are crucial components in systems where precise motor control is required. They are used in diverse applications, including CNC machines, 3D printers, industrial automation, drones, and electric vehicles. The choice of a motor control PCB depends on the specific motor type, voltage and current requirements, and the level of control needed for the application. These PCBs are essential for achieving optimal performance and efficiency in motor driven systems. If you have any question, please contact KUKEfor more imformation.